Would you like to learn more about insert molding, and how it varies from other plastic injection molding applications?
Insert molding is like over molding in that metal components are placed into the cavity of the mold prior to molding. An operator may manually position inserts inside the mold. A robotic arm can also be used to precisely spot inserts. The mold then closes, and plastic is molded around the insert, creating a single, combined plastic part.
It is an effective method to join separate components into a finished piece. Often the inserts are threaded which allows parts to be mated into a final assembly. By utilizing metal inserts, part weight can be reduced and provide greater durability.
How Metal Insert Molding Is Made
Insert molding is sometimes called metal insert molding or metal brass/screw molding. To efficiently use this application, one must ensure that you are choosing the right material that provides the best mechanical and chemical bonding to meet requirements.
Here are some industries that employ insert molding in their products:
- Medical
- Agriculture
- Construction
- Toys
- Solar
- Electronics
- Consumer Products
- Cookware
- Handheld and Wearable Devices
- Safety
- Defense
- Pharmaceutical
- Automotive
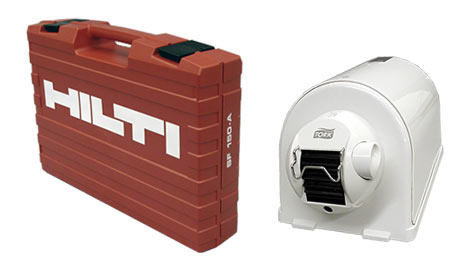
Insert Molding is Growing FAST
Today insert molding allows you to create a unique variety of products that are a strong combination of metal and plastic depending on what applications you may have. As the products we use in our daily lives get more and more sophisticated, so does the demand for insert molding manufacturing. Our company has been at the forefront of plastic injection molding for many decades and is here ready to answer any of your questions and to help you with your next plastic manufacturing project! Call our director of sales Steven Ames at 209-497-4290 if you’d like to learn more.